People
Up to 20% of the manufacturing process is allocated to human inspections only. This dependency leads to other limitations in the overall process.
- Limited visibility into real-time operations and performance
- Inconsistent defect detection which can vary from one inspector to another.
- Complete reliance on human observation and an increased risk of oversight.
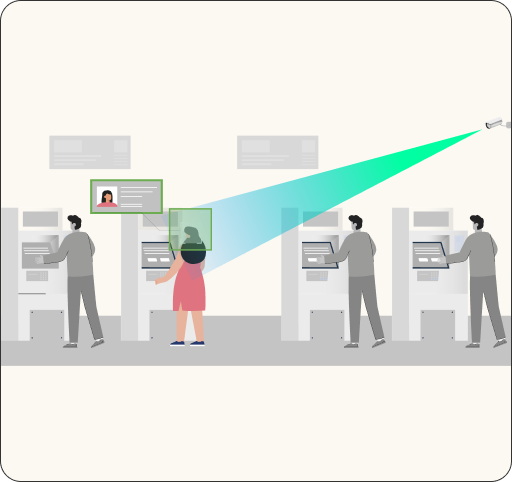
Production
Human inspection leads to a 5-10% error rate on average. Compromised product quality and delayed responses are common as a result of this.Â
- Difficulty detecting micro-level defects invisible to the human eye.Â
- Inconsistent defect detection which can vary from one inspector to another.
- Delays in corrective measures which impact production timelines.
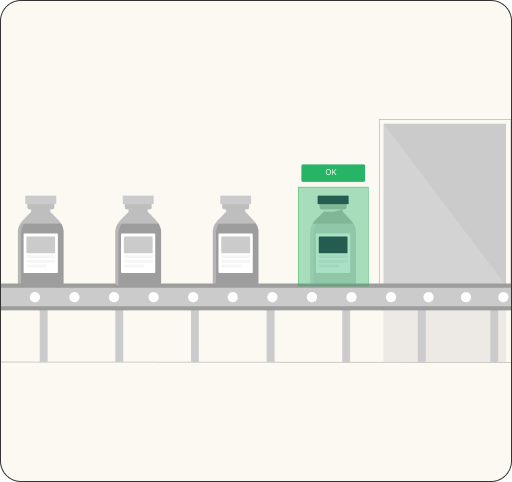
ProductivityÂ
Manual inspections can slow production by up to 30%. It’s a bottleneck in itself which also inflates the costs.Â
- Labor-intensive processes demand significant resources.Â
- Manual methods hinder scalability and create operational bottlenecks.Â
- Increasing labor costs directly impact profitability.Â
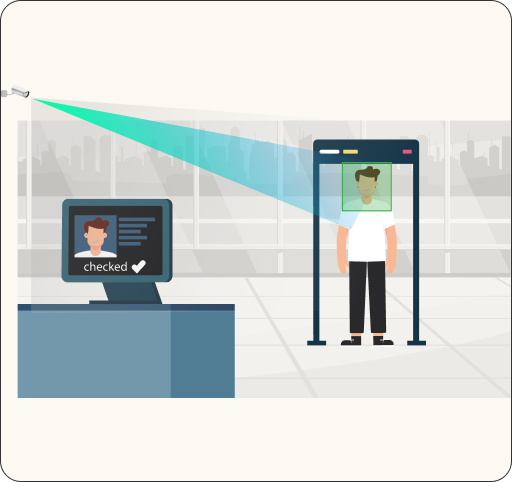
ProtectionÂ
Workplace injuries can cost a company up to four times an injured worker’s annual salary. Safety is non-negotiable but effective, 24/7 monitoring is a challenge.Â
- Workers often fail to adhere to safety protocols, increasing risks.Â
- Achieving 360-degree security coverage is difficult with current systems.Â
- Inability to meet 100% compliance with safety standards exposes organizations to liabilities.Â
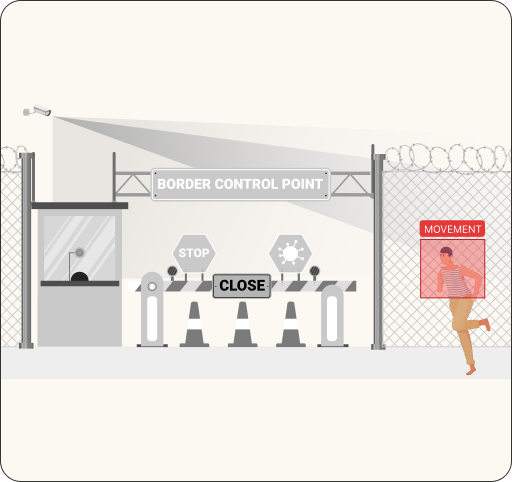